Automotive gears are critical components that endure extreme loads, friction, and stress during vehicle operation. The ability of these gears to withstand such conditions is largely determined by their hardness—a material property that measures resistance to deformation, wear, and fatigue. The degree of hardness of a gear is crucial in determining how long it will last, how well it functions, and whether or not it will fail when subjected to heavy usage.
Having a thorough understanding of hardness is a necessity for automotive manufacturers, as it directly influences gear efficiency and reliability. As part of this article, we will explore the different hardness testing methods, such as Rockwell, Vickers, and Brinell, that are commonly used in the manufacturing of automotive gears. Moreover, we will examine how these tests contribute to the durability and performance of gears, assuring compliance with industry standards.
Hardness Testing Methods for Automotive Gears
Let us discuss 3 of the most commonly used hardness testing methods in automotive gear manufacturing: Rockwell, Vickers, and Brinell. All of these methods, each with its own advantages and applications, are crucial to understanding how materials respond to stress. Our goal is to shed light on the significance of each of these testing methods in determining the reliability and longevity of automotive gears by examining each in detail.
Rockwell Hardness Test
The Rockwell hardness test is one of the most widely used methods in automotive gear manufacturing, particularly for materials like case-hardened steels, which are commonly used in gear production. The Rockwell test measures the depth of penetration of an indenter under a specific load, providing an easy-to-read numerical value that represents the material’s hardness. This test is highly appreciated for its speed, simplicity, and reliability.
There are several Rockwell scales, but for automotive gears, Rockwell C (HRC) and Rockwell Superficial (HR15N) are the most commonly used. The Rockwell C scale (HRC) is typically used for harder materials like case-hardened steel, with hardness values ranging from 20 to 70 HRC, where higher values indicate greater hardness. For softer materials or thin case-hardened layers, the Rockwell Superficial scale is often employed, providing measurements that are ideal for smaller or thinner components.
In the Rockwell test, the process involves applying an initial load, followed by a major load, which is held for a set period. The indenter penetration depth is then measured, and a hardness number is calculated based on the depth. The Rockwell C scale is especially useful for determining the hardness of gears used in high-load applications, such as automotive transmissions, differentials, and powertrains.
Vickers and Microhardness Testing
The Vickers hardness test is another method used extensively in automotive gear production, especially when high precision is required. The Vickers test measures the size of an indentation left by a diamond pyramid indenter, which applies a specific load for a set time. This test is particularly useful for measuring hardness in carburized gears, where the case depth (the hardened surface layer) needs to be accurately assessed.
The Vickers test provides a detailed hardness profile by measuring the diagonal lengths of the indentation, and the hardness value is calculated using the applied load and the size of the indentation. It can be used for both thin layers, like in nitrided or induction-hardened gears, and thicker materials. The Vickers test has the advantage of providing precise, consistent results regardless of the thickness of the material.
For even more precision, microhardness testing can be performed, typically using the Knoop or Vickers (HV) scales, which measure smaller, shallower indentations. The Vickers scale (HV), for example, is used with loads ranging from 0.2 to 1000 grams, ideal for assessing the hardness of very thin hardened layers in gears. The ability to assess case depth with high precision makes the Vickers test a valuable tool for automotive manufacturers focused on optimizing gear performance and durability.
Brinell Hardness Test
The Brinell hardness test is often used for automotive gears made of larger or softer materials, such as cast iron or Austempered Ductile Iron (ADI). The Brinell test uses a steel or tungsten carbide ball indenter, which is pressed into the material surface under a specific load. The size of the indentation left by the ball is then measured, and the hardness is calculated based on the applied force and the area of the indentation.
The Brinell test is particularly useful for evaluating the hardness of bulk materials and the uniformity of the material’s microstructure. It is frequently used for larger gears, as the indentation depth is more suitable for coarser materials like cast iron, which can be challenging to test using more sensitive methods like Rockwell or Vickers. For materials with rough or uneven surfaces, the test is typically performed using loads between 500 and 3000 kgf.
Why Hardness Testing is a Must in Automotive Gears
As we mentioned earlier, hardness testing is an integral part of the manufacturing process of automotive gears, as it directly affects the durability, efficiency, and safety of the gears that are used in the vehicles.
The Role of Hardness in Gear Performance
The hardness of a gear determines its resistance to wear, which is critical to guaranteeing gear longevity under operational conditions. Gears operate in high-stress environments where friction and pressure are constantly applied. If the material hardness is too low, the gear will wear out more quickly, leading to frequent repairs or replacements. On the other hand, if the hardness is too high, the gear may become brittle, making it prone to cracking under stress.
For example, consider the gears in heavy-duty trucks used in transportation. These vehicles often operate under extreme loads, especially in long-distance hauling. If the gears in the drivetrain or transmission system are made from inadequate hardness material, they may fail prematurely. This failure could result in loss of power, overheating, and even complete mechanical failure. In such cases, repairs are costly, and downtime can significantly impact truck operational efficiency. More critically, if such a failure happens in public vehicles like buses or trains, it could lead to accidents, putting passengers at risk.
The Importance of Standards Compliance in Automotive Gear Manufacturing
Compliance with international standards is crucial in automotive gear manufacturing to ensure that gears meet the necessary hardness specifications for safety and durability. Standards like ISO 6506 and ASTM E10 provide detailed guidelines that manufacturers follow to test and verify gear hardness, helping to achieve optimal performance in demanding applications. Regardless of the industry, these standards are more than just recommendations – they are crucial for preventing failures, enhancing product longevity, and maintaining product safety.
ASTM E10, which outlines the Brinell hardness testing method, is another vital standard in gear manufacturing. The Brinell test provides a reliable measurement of a material’s resistance to deformation, thus contributing to the success of gear production. For materials like case-hardened steel and cast iron, compliance with ASTM E10 makes certain that the gears will perform under operational stresses, providing reliable service without breaking down prematurely.
Achieving Reliable Hardness Testing for Automotive Gear Manufacturing
To achieve reliable and consistent hardness testing results, several important factors must be carefully considered throughout the process. These factors all contribute to the accuracy and reliability of measurements, ultimately contributing to the overall quality and performance of automotive gears. Here are the key elements of precise hardness testing:
1. Proper Sample Preparation
Preparation of the gear surface is one of the first steps to achieving accurate hardness testing. The test surface must be clean, smooth, and free of contaminants like oil, rust, or dirt. Surface irregularities, such as scratches or burrs, can affect the indentation process and lead to erroneous results. Additionally, gears that are improperly prepared, with rough or uneven surfaces, will result in inaccurate measurements. A well-prepared sample guarantees that the hardness tester’s indenter can make precise, consistent impressions on the gear surface.
2. Selection of the Right Test Method
Different hardness testing methods are suited to different materials and applications. It is crucial to select the right test based on the gear material, the required precision, and the application. For instance, Rockwell tests are ideal for quick and general hardness assessments of case-hardened steels, while Vickers tests provide more detailed, high-precision results for carburized or nitrided gears, particularly when assessing case depth. The Brinell test is appropriate for larger gears or soft materials. The appropriate test method assures that the measurement is relevant and reliable for the type of gear being tested.
3. Test Load and Indenter Selection
The choice of indenter and applied load is critical to achieving reliable results. For instance, the Rockwell C scale (HRC) uses a diamond cone indenter and is ideal for hard materials, whereas the Brinell test uses a steel or tungsten carbide ball to make impressions on softer materials. The test load must also be appropriate for the material being tested; too high or too low a load can damage the surface or fail to create a discernible indentation. The calibration of the load system is a necessity to obtaining accurate and consistent readings.
4. Environmental Conditions
The environment in which hardness testing is conducted can significantly impact the results accuracy. Temperature and humidity can affect gear material properties, altering hardness. Extreme heat can soften some materials, while excessive moisture can corrosion. Therefore, it’s essential to test hardness in a controlled environment to prevent external factors from influencing the results.
5. Consistent Calibration and Quality of Testing Equipment
Regular calibration of testing machines is another necessary step to obtain accurate hardness measurements. Over time, wear or mechanical changes can affect precision, so using certified calibration standards like Rockwell or Brinell test blocks is necessary to verify equipment accuracy. Equally important is the quality of the equipment itself. High-quality, well-maintained testers, such as modern Rockwell, Vickers, and Brinell hardness testers, facilitate consistent load application and precise measurement, minimizing errors. Advanced features like digital readouts and automation further improve accuracy and repeatability. By combining consistent calibration and reliable, high-quality equipment, automotive gears are guaranteed to meet safety and performance requirements.
NG-RockGen DGEN Series – Rockwell Hardness Tester for Accurate Measures
When discussing the importance of reliable hardness testing, we cannot overlook the significance of high-quality equipment in achieving precise and consistent results. One such example is our NG-RockGen DGEN Series – Digital Rockwell Hardness Tester. This advanced digital hardness tester was created to meet the rigorous demands of automotive gear manufacturing, where precise hardness measurements are critical for guaranteeing gear performance, durability, and safety.
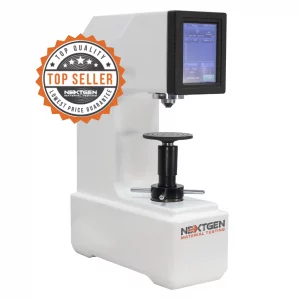
The NG-RockGen DGEN Series offers a range of Rockwell scales, including regular, superficial, and TWIN models, providing multiple options for testing various gear materials with precision. With models capable of testing materials such as case-hardened steels, alloys, and aluminum, the NG-RockGen DGEN makes certain that gears in automotive applications are tested for hardness in compliance with industry standards, such as ASTM E18 and ISO 6508.
Equipped with a digital LCD display and high repeatability, this tester offers easy-to-read results, significantly reducing human error and ensuring reliable, consistent data. Automatic testing procedures and high-resolution measurements (with accuracy up to 0.001) make it an ideal choice for manufacturers who need to confirm that their gears meet exact hardness specifications. With its unrivaled dependability and reliability, the NG-RockGen DGEN Series offers long-term value for automotive gear production, whether you are testing transmissions, differentials, or powertrains.
Achieving Reliable Automotive Gear Performance Through Hardness Testing
Automotive gear manufacturing cannot ignore hardness testing. The ability to withstand extreme loads, friction, and pressure directly impacts the performance and longevity of gears used in a number of applications, from transmissions to differentials. By accurately measuring gear hardness, manufacturers ensure durable, reliable, and safe gears for use in vehicles operating under challenging conditions.
Selection of the right testing method, proper sample preparation, and maintaining high-quality, calibrated testing equipment are all key to accurate and repeatable results. Hardness testing is not just about assessing material strength—it is about preventing costly failures, improving operational efficiency, and guaranteeing the safety of the vehicle and its passengers. Through these tests, manufacturers are able to comply with industry standards, providing proof that their products perform consistently and meet the highest quality standards.
At the heart of it all is the need for reliable equipment and precise testing procedures. Gear performance and longevity are shaped by how well these testing steps are carried out. For manufacturers aiming to deliver top-quality automotive gears, investing in dependable hardness testing equipment and maintaining rigorous testing protocols are crucial steps toward long-term success.
We are here to help you meet all your material testing requirements by providing advanced material testing tools. If you are interested in new products for hardness testing, please take a closer look at our metal testing equipment. If you need more assistance or have specific inquiries, feel free to contact us directly or request an online quote.