Get Your Material Testing Equipment Certified
Ensuring compliance with material testing standards is essential for achieving accurate, repeatable, and industry-approved results. At NextGen Material Testing, we provide high-precision testing equipment and facilitate certification services for both our products and third-party devices, ensuring full compliance with NADCAP, ISO, ASTM, and other regulatory standards.
Moreover, at NextGen Material Testing, we work with trusted accreditation partners to help laboratories and manufacturers meet, but not limited to, ISO/IEC 17025:2017 requirements for calibration and testing competence. For organizations requiring compliance with, but not limited to, ANSI/NCSL Z540-1-1994, we offer certification assistance to ensure that calibration procedures meet the stringent requirements for measurement accuracy and traceability.
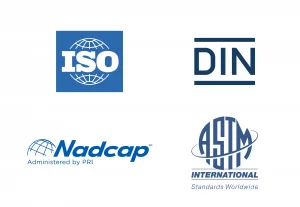
ASTM E4 & ISO 7500-1
If you use force measurement equipment and require compliance with ASTM E4 (Class A) or ISO 7500-1 (Class 0.5 or 1), NextGen Material Testing can facilitate the certification process for both our equipment and third-party instruments. These standards establish strict accuracy requirements for force verification, ensuring that your universal testing machines (UTMs), load cells, and force measurement devices meet rigorous calibration and performance criteria. With our expertise and ISO accredited partners, we help your facility achieve full compliance with NADCAP, ISO, and ASTM regulations, guaranteeing precise, repeatable, and accredited force measurement capabilities across metallurgical, aerospace, automotive, and industrial applications.
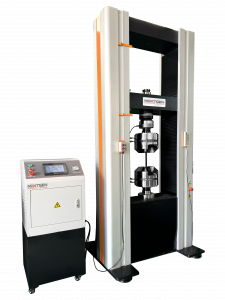
ASTM E83 & ISO 9513 standards for Extensometers/COD Gage/Deflectometers
Ensuring accurate strain measurement is critical for materials testing, and compliance with ASTM E83 and ISO 9513 is essential for verifying the performance of extensometers, crack opening displacement (COD) gages, and deflectometers. These standards define accuracy classifications, calibration procedures, and performance verification to guarantee precise, repeatable, and traceable strain measurements across a wide range of testing applications.
At NextGen Material Testing, we facilitate the calibration and verification of extensometers and strain measurement devices, ensuring compliance with ASTM E83 (for axial and transverse extensometers) and ISO 9513 (for displacement and strain-measuring devices in tensile, compression, and flexural testing). Our services cover direct verification, linearity assessments, and accuracy classification to meet the stringent requirements of aerospace, automotive, metallurgical, and industrial laboratories.
With access to ISO & ASTM-accredited calibration services, we support accreditation for both NextGen’s extensometers and third-party devices, providing fully traceable calibration reports that help laboratories meet ISO and ASTM certification requirements. Whether you require verification for extensometers, COD Gage, or deflectometers, our expertise ensures that your testing equipment delivers consistent, audit-ready results for tensile, flexural, and fatigue testing applications.
Contact NextGen today to ensure your extensometers and strain measurement systems meet the highest industry standards for accuracy and compliance.
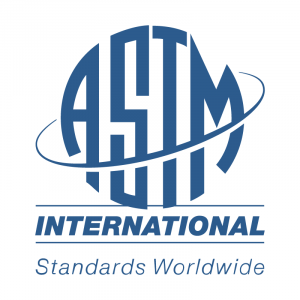
ASTM E1951 for Microscopes / Vision Systems
Precision imaging is essential in materials testing, failure analysis, and quality control, and compliance with ASTM E1951 ensures that microscopes, vision systems, and optical measuring instruments deliver accurate and repeatable measurements. This standard defines procedures for calibrating optical and digital imaging systems, ensuring measurement accuracy for dimensional analysis, surface inspection, and microstructural evaluation in industries such as metallurgy, aerospace, medical device manufacturing, and electronics.
At NextGen Material Testing, we facilitate calibration and verification for microscopes, vision systems, and other optical measurement tools, ensuring compliance with ASTM E1951 standards for magnification accuracy, field distortion, and dimensional measurement precision. Our services cover direct verification, resolution assessments, and optical system validation, helping laboratories achieve reliable, traceable, and audit-ready imaging results.
With access to ASTM-accredited calibration services, we provide certification not only for NextGen’s imaging and vision systems but also for third-party optical devices. Whether you use high-magnification metallurgical microscopes, digital measurement systems, or automated vision inspection tools, we ensure that your equipment meets ASTM accreditation requirements for high-precision industrial and research applications.
Contact NextGen today to ensure your microscopes and vision systems meet the highest standards for accuracy, compliance, and performance.
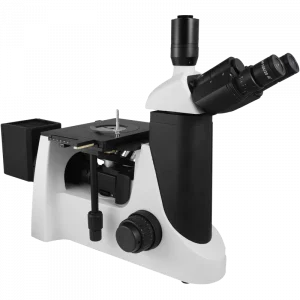
ASTM D2240 for Rubber Property Durometer Hardness
If you require durometer hardness testing for rubber, elastomers, and soft materials, compliance with ASTM D2240 and ISO 21509 is essential to ensure accurate, repeatable, and traceable hardness measurements. These standards define the calibration, verification, and testing procedures for Shore hardness testers, ensuring precise measurement of rubber, plastics, and flexible materials used in automotive, aerospace, and industrial applications.
At NextGen Material Testing, we provide ASTM and ISO-accredited calibration and certification services for both our durometers and third-party devices, ensuring compliance with ASTM D2240 and ISO 21509 requirements. Our expertise guarantees that your hardness testing equipment meets strict industry standards, delivering consistent, audit-ready results for material quality control, research, and production testing.
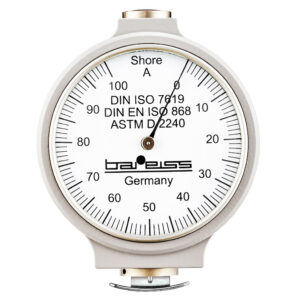
ISO 4545-2 for Indirect Calibration Vickers/Knoop
If you require indirect calibration for Vickers and Knoop hardness testers, compliance with ISO 4545-2 is essential to ensure accurate and repeatable hardness measurements. This standard specifies the procedures for verifying test force application, indentation accuracy, and optical measurement consistency, ensuring that your equipment meets global calibration and traceability requirements. At NextGen Material Testing, we facilitate ISO 4545-2-compliant calibration and certification services for both our hardness testers and third-party devices, working with ISO-accredited partners to guarantee full compliance. Whether for metallurgical analysis, coatings testing, or precision material research, we help laboratories achieve ISO and other industry certification, ensuring audit-ready, reliable, and high-precision hardness testing results.
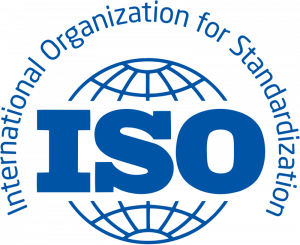
ASTM E2428/E2624, ISO 6789-2 and DIN 51309 for Calibration of Torque Testing Machines
If you require calibration for torque testing machines, compliance with ASTM E2428, ASTM E2624, ISO 6789-2, and DIN 51309 ensures precise, repeatable, and traceable torque measurements across industrial, aerospace, and automotive applications. These standards establish requirements for torque transducer accuracy, calibration procedures, and verification of torque measurement systems, ensuring that your torque testing equipment meets strict global compliance standards.
At NextGen Material Testing, we provide ISO, ASTM and DIN accredited calibration and certification services for both our torque testers and third-party systems, covering torque wrenches, transducers, and calibration benches. We guarantee industry compliance, ensuring your equipment delivers high-precision torque verification, audit-ready calibration data, and consistent measurement performance for quality control, research, and production environments.
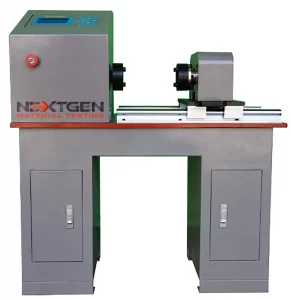
ASTM E384 for High Magnification Microscope
If you use high-magnification microscopes for microhardness testing, compliance with ASTM E384 is essential to ensure accurate, repeatable, and traceable results. This standard defines the calibration and verification requirements for microscopes used in Vickers and Knoop hardness testing, focusing on optical measurement precision, indentation analysis, and magnification accuracy. At NextGen Material Testing, we facilitate certification and calibration services for both our microscopes and third-party optical systems, ensuring compliance with ASTM E384. NextGen helps laboratories achieve global industry ASTM compliance, guaranteeing that high-magnification microscopy systems deliver precise and consistent microhardness measurements for metallurgical research, coatings analysis, and quality control applications.
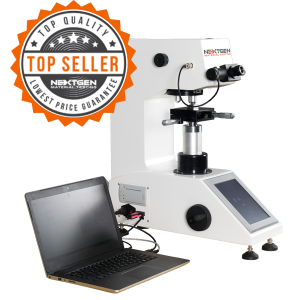
Additel 222A for Electrical Simulation of Thermocouple Indicating Devices
If you require electrical simulation for thermocouple indicating devices and need compliance with Additel 222A calibration standards, we can facilitate the certification process not only for the equipment you purchase from us but also for third-party instruments. The Additel 222A is essential for accurate temperature simulation and verification, ensuring that thermocouple-based measurement systems meet precision requirements for industrial and laboratory applications. With our experience, we help you achieve full compliance with industry standards, ensuring accurate, repeatable, and traceable calibration for quality control, aerospace, and Additel 222A testing environments.
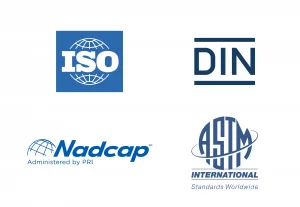
ASTM E74 (Class AA) or ISO 376 (Class 00, 0.5, or 1)
If your force measurement equipment is used for tension and compression testing and requires compliance with ASTM E74 (Class AA) or ISO 376 (Class 00, 0.5, or 1), NextGen Material Testing can facilitate certification and calibration services for both our equipment and third-party devices. These standards define the accuracy and calibration requirements for load cells, proving rings, and reference force transducers, ensuring traceable and reliable force application in materials testing and calibration laboratories. With our knowledge and ASTM/ISO-accredited partners, we help your facility achieve compliance and full industry accreditation, ensuring that your tension and compression testing systems meet the highest precision requirements for quality control, research, and industrial applications.
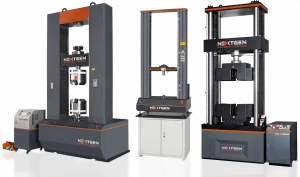
ASTM E1012, ASTM E2309 & ASTM E2658
If you require alignment calibration, displacement measurement, or verification tools for material testing systems, we can assist in obtaining certification not only for the equipment you purchase from us but also for third-party instruments.
- ASTM E1012 ensures precise alignment calibration for testing frames, reducing measurement errors in tensile, compression, and fatigue testing.
- ASTM E2309 covers digital indicator calibration for cable extension transducers, ensuring accurate displacement measurements in test frames.
- ASTM E2658 applies to cable extension transducers with stopwatch verification, ensuring traceable measurement accuracy for displacement tracking.
- Calibrated extensometers within ASTM Class B1 range and Class A stopwatches provide high-precision strain measurement, essential for tensile and elongation testing.
- Load cells calibrated to Class A standards, combined with stopwatches, ensure accurate force measurement in compliance with NADCAP and global testing standards.
- Feeler gauges and straight edges play a vital role in verifying test frame alignment, ensuring mechanical integrity and precision in material testing applications.
NextGen’s expertise can help your laboratory achieve full compliance with ASTM accreditation requirements, ensuring precision, repeatability, and regulatory compliance for force measurement, alignment calibration, and extensometry applications.
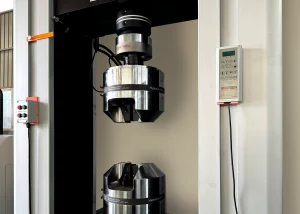
ASTM E18, ASTM E3246, ISO 6508-2, DIN 50157-2 for Direct Verification of Rockwell Hardness Testing Machines
If you require direct verification of Rockwell hardness testing machines, compliance with ASTM E18, ASTM E3246, ISO 6508-2, and DIN 50157-2 is essential to ensure accurate, repeatable, and traceable hardness measurements. These standards establish the calibration, force application verification, indentation accuracy, and performance validation requirements necessary for Rockwell hardness testers used in metallurgical, aerospace, automotive, and industrial applications.
At NextGen Material Testing, we provide ASTM, ISO and DIN-accredited calibration and certification services for both our Rockwell hardness testers and third-party equipment, ensuring full compliance with ASTM, ISO, and DIN regulations. Our expertise guarantees that your hardness testing system meets strict industry standards, delivering consistent, audit-ready results for quality control, research, and production testing environments.
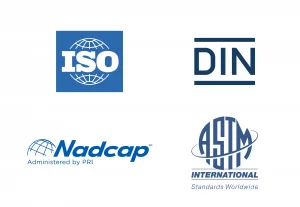
Indirect verification per ASTM E18 for Hardness Testers Rockwell
If you use Rockwell hardness testers and require indirect verification per ASTM E18, we can facilitate certification not only for the equipment you purchase from us but also for third-party instruments. ASTM E18 establishes the requirements for calibrating and verifying Rockwell hardness testers through indirect verification, ensuring that your system delivers accurate, repeatable, and traceable hardness measurements.
This process involves testing certified reference blocks to assess the tester’s performance, repeatability, and error limits, guaranteeing compliance with ASTM and industry regulations. We can help your facility achieve full ASTM E18 compliance, ensuring your Rockwell hardness testing process meets the highest standards for quality control, material validation, and industrial applications.
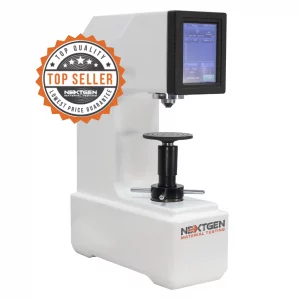
Indirect verification method per ISO 6506-2, ASTM E10 for Hardness Testers Brinell
If you use Brinell hardness testers and require indirect verification per ISO 6506-2, ASTM E10, or ASTM E103, we can facilitate certification not only for the equipment you purchase from us but also for third-party instruments. These standards define the calibration and verification procedures for Brinell hardness testing systems, ensuring accuracy, repeatability, and compliance with industry regulations.
The indirect verification process involves testing certified Brinell hardness reference blocks to assess machine performance, indentation accuracy, and force application. This guarantees that your Brinell hardness tester meets ISO & ASTM and global quality control requirements for metallurgical, aerospace, and industrial applications.
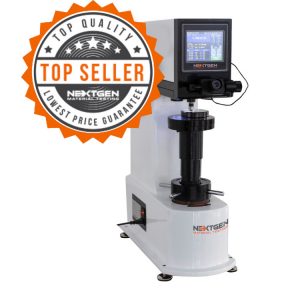
ASTM A956 for Leeb Hardness Testers
If you use Leeb hardness testers and require compliance with ASTM A956, we can facilitate certification not only for the equipment you purchase from us but also for third-party instruments. ASTM A956 establishes the verification and calibration requirements for portable Leeb hardness testers, ensuring accurate, repeatable, and traceable hardness measurements in field and laboratory environments.
This standard covers the indirect verification process, which includes testing against certified reference materials to assess impact device accuracy, rebound velocity, and hardness value consistency. Let us help your facility achieve full ASTM A956 compliance, ensuring that your Leeb hardness testing process meets industry standards for quality control and material validation.
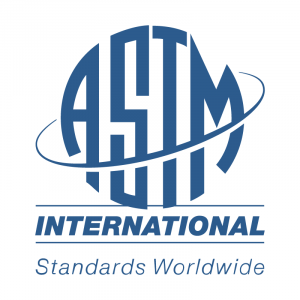
Indirect verification method per ASTM E92, ISO 6507-2 for Microindentation Hardness Testers (Knoop & Vickers)
If you use microindentation hardness testers (Knoop & Vickers) and require indirect verification in accordance with ASTM E92 or ISO 6507-2, we can assist in obtaining certification not only for the equipment purchased from us but also for third-party devices. These standards establish the calibration and verification procedures necessary to ensure high-precision, repeatable, and traceable microhardness measurements across a wide range of materials.
The indirect verification process involves using certified reference blocks to evaluate indentation accuracy, load application consistency, and optical measurement precision. Ensuring compliance with ASTM and ISO requirements, this process guarantees that your Knoop and Vickers hardness testers deliver accurate, reliable, and standardized hardness values for thin coatings, metallurgical analysis, and high-precision material testing.
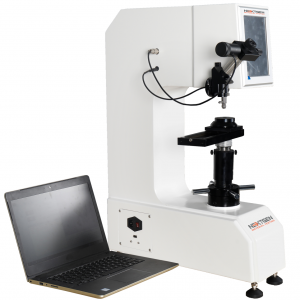
ASTM E23 and ISO 148-2 for Indirect Verification of Charpy Impact Testers
If you use Charpy impact testers and require indirect verification in accordance with ASTM E23 or ISO 148-2, we can facilitate certification not only for the equipment you purchase from us but also for third-party machines. These standards define the verification and calibration procedures necessary to ensure accurate, repeatable, and traceable impact energy measurements in material toughness testing.
The indirect verification process involves testing with certified reference specimens to evaluate impact energy absorption accuracy, pendulum alignment, and test repeatability. Compliance with ASTM E23 and ISO 148-2 ensures that your Charpy impact tester meets ASTM and ISO global quality control standards, guaranteeing precise fracture analysis and reliable material toughness evaluations. NextGen will help your facility maintain full regulatory compliance, ensuring consistent and accurate impact testing performance across various industrial applications.
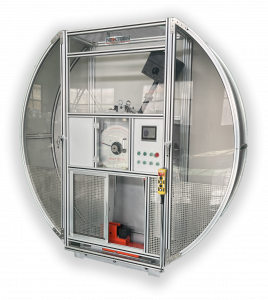
ASTM E23 & ISO 148-2 for Direct Verification of Charpy Impact Testers
If you require direct verification of Charpy impact testers in accordance with ASTM E23 and ISO 148-2, we can assist in obtaining certification not only for the equipment you purchase from us but also for third-party machines. These standards establish the procedures for evaluating mechanical components, including pendulum alignment, striker geometry, anvil positioning, and energy scale accuracy to ensure precise and repeatable impact testing. Compliance with ASTM E23 and ISO 148-2 guarantees that your Charpy impact tester meets industry requirements, ensuring reliable material toughness analysis and fracture evaluation. Our expertise will allow you to achieve full regulatory compliance, minimizing testing variability and maximizing accuracy in critical impact assessments.
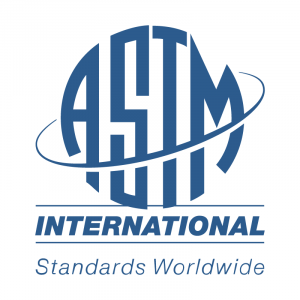
ASTM E18, ISO 6508-2, ASTM E92, ISO 6507-2 for Direct Verification Calibration For Rockwell, Brinell and Vickers
If you require direct verification calibration for Rockwell, Brinell, and Vickers hardness testing machines, compliance with ASTM E18, ISO 6508-2 (Rockwell), ASTM E92, and ISO 6507-2 (Brinell & Vickers) is essential to ensure accuracy, repeatability, and traceability in hardness measurement. These standards define the calibration, force application verification, indentation accuracy, and overall performance requirements necessary for maintaining high-precision hardness testing equipment in metallurgical, aerospace, automotive, and industrial applications.
At NextGen Material Testing, we provide ISO & ASTM-accredited calibration and certification services for both our hardness testers and third-party systems, ensuring full compliance with ASTM, ISO, and industry regulations. We guarantee that your Rockwell, Brinell, and Vickers hardness testing machines deliver reliable, audit-ready results, supporting quality control, research, and production testing requirements with confidence.
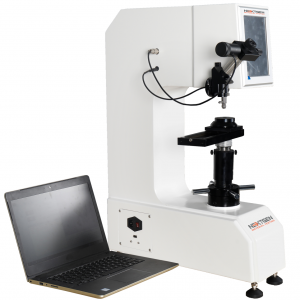
ANSI/NCSL Z540-1-1994
If you require precision calibration and measurement traceability, compliance with ANSI/NCSL Z540-1-1994 is essential to ensure accuracy, reliability, and standardization in testing and calibration laboratories. This standard establishes the requirements for calibration system accuracy, documentation, and traceability to national or international standards, making it critical for aerospace, defense, automotive, and industrial applications where high-precision measurements are required.
At NextGen Material Testing, we work with ISO, ASTM, DIN, NADCAP, ANSI-accredited partners to facilitate ANSI/NCSL Z540-1-1994-compliant calibration and certification services for both our testing equipment and third-party devices. Whether you need verification for force measurement systems, hardness testers, extensometers, or dimensional measuring instruments, our expertise ensures audit-ready, traceable, and fully compliant calibration solutions that meet strict industry and regulatory requirements.
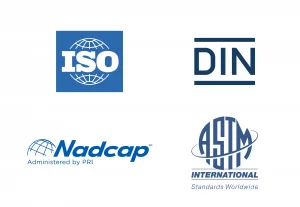
ASME B89.1.14-2018 for Calipers
If you require calibration and verification of calipers, compliance with ASME B89.1.14-2018 is essential to ensure precise, repeatable, and traceable dimensional measurements. This standard defines the accuracy, performance, and calibration requirements for digital, dial, and vernier calipers, ensuring they meet strict metrology and quality control standards in aerospace, automotive, manufacturing, and research applications.
At NextGen Material Testing, we provide ASME-accredited calibration and certification services for both our calipers and third-party measuring instruments, ensuring full compliance with ASME B89.1.14-2018 and global industry standards. We guarantee that your calipers deliver precise and audit-ready measurements, supporting reliable quality control, production efficiency, and laboratory accuracy.
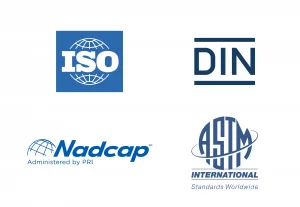
ISO/IEC 17025:2017
At NextGen Material Testing, we work with trusted accreditation partners to help laboratories and manufacturers meet ISO/IEC 17025:2017 requirements for calibration and testing competence. This standard ensures that testing and calibration laboratories demonstrate technical proficiency, traceability, and reliable measurement uncertainty calculations.
We facilitate ISO 17025-compliant calibration and certification services for tensile testing machines, force measurement systems, extensometers, and alignment verification tools, whether purchased from us or third-party suppliers. Our supplied accreditation details include ISO 17025 credentials, ensuring full traceability and regulatory compliance, mirroring the industry-standard scope of accredited laboratories such as Cal-Rite (valid until October 31, 2026).
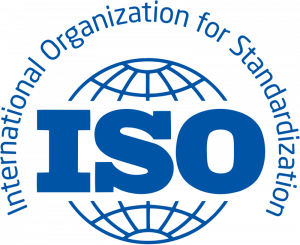
NADCAP
The National Aerospace and Defense Contractors Accreditation Program (NADCAP) is an industry-managed certification designed to ensure high standards in the aviation, space, and defense sectors. Established in 1990 and administered by the Performance Review Institute (PRI), NADCAP creates a standardized approach to auditing and accreditation, reducing redundant supplier assessments while improving overall quality. By bringing together technical experts, suppliers, and OEMs, NADCAP defines strict audit criteria that streamline compliance, enhance safety, and reduce costs for manufacturers across the aerospace and defense supply chain.
Why NADCAP Accreditation Matters
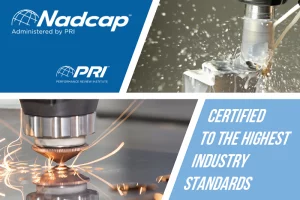
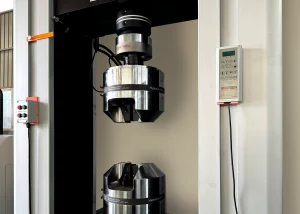
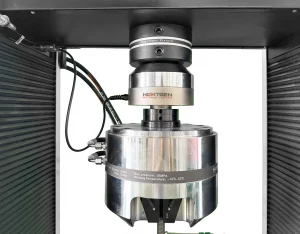
NADCAP accreditation is a mark of excellence in aerospace and defense manufacturing. Companies that achieve NADCAP compliance demonstrate their commitment to:
- Quality Assurance – Meeting the strictest industry standards
- Process Standardization – Reducing variability in manufacturing.
- Operational Efficiency – Eliminating redundant audits, saving time and costs.
- Global Recognition – Boosting credibility with aerospace and defense leaders.
- Increased Business Opportunities – Positioning suppliers for contracts with top-tier OEMs.
According to the Performance Review Institute’s Supplier Satisfaction Survey, over 90% of responders believe NADCAP accreditation has added value to their organization.
The NADCAP Audit Process
NADCAP certification follows a structured process to ensure compliance with industry-specific manufacturing standards:
1. Registration & Scheduling
- Suppliers register on PRI’s eAuditNet platform.
- Audits are scheduled 6-9 months in advance to allow preparation.
2. Pre-Audit Preparation
- Suppliers conduct a self-audit based on NADCAP’s official audit criteria.
- Process improvements and corrections are made before the formal audit.
3. On-Site Audit
- An industry-approved auditor evaluates the supplier’s processes.
- Daily reviews highlight findings, and a final report is prepared.
4. Compliance Review
- Suppliers address non-conformances, with guidance from PRI’s technical staff.
- A final audit report is reviewed by NADCAP Task Groups, which include experts from major aerospace and defense companies.
5. Accreditation & Reassessment
- If compliance is met, NADCAP certification is granted.
- Ongoing audits and reevaluations ensure continued adherence to standards.
Which Processes Require NADCAP Certification?
NADCAP accreditation covers a wide range of critical aerospace and defense manufacturing processes, including:
- Non-Destructive Testing (NDT)
- Heat Treating
- Materials Testing Laboratories
- Welding
- Coatings & Surface Enhancement
- Chemical Processing
- Additive Manufacturing
- Electronics & Fluid Distribution Systems
Benefits of NADCAP Accreditation for Suppliers
Only the most qualified suppliers achieve NADCAP certification. By obtaining accreditation, companies gain:
- Stronger Customer Relationships – OEMs recognize NADCAP as a sign of trust and quality.
- Fewer Redundant Audits – One NADCAP audit replaces multiple individual customer audits.
- Reduced Defect Rates – Studies show NADCAP-certified suppliers experience fewer manufacturing defects.
- Competitive Advantage – Many aerospace and defense contracts require NADCAP certification.
- New Business Opportunities – Access to global markets and high-profile contracts.
How NextGen Material Testing Helps You Get NADCAP Ready
Achieving NADCAP accreditation requires rigorous and consistent testing to meet strict industry standards. NextGen Material Testing provides Universal Testing Machines engineered for tensile, compression, and bending tests in aerospace and defense applications—all in compliance with NADCAP requirements. Contact us today to request a detailed quotation for a system designed to secure your NADCAP certification
NADCAP Certified-ready products:
NextGen provides a specialized NADCAP-compliant alignment device that ensures optimal coaxiality of ≤ 5%, meeting ASTM E1012 and NASM 1312B standards. This precision alignment reduces testing variability, helping laboratories meet NADCAP audit requirements with confidence.
Key Features of Our NADCAP-Ready Testing System:
- Precision Alignment: Reduces misalignment errors for superior test accuracy.
- Versatile Application: Designed for tensile, compression, and bending tests.
- Reliable Results: Ensures consistent and repeatable performance for compliance.
With this universal testing machine precision upgrade, your lab will be NADCAP ready, ensuring compliance, quality, and industry leadership.
For more information on NADCAP compliance and how NextGen Material Testing can support your accreditation journey, contact us today.
Certification Ready Equipment
At NextGen Material Testing, we facilitate calibration and certification services for both our equipment and third-party devices, ensuring full compliance with NADCAP, ISO, ASTM, and ISO/IEC 17025:2017 standards. We support certification for universal testing machines, force measurement systems, hardness testers, impact testers, extensometers, and alignment verification systems, covering ASTM E4 (force verification), ASTM E1012 (alignment calibration), ASTM E83 & ISO 9513 (extensometer calibration), ISO 7500-1 (force measurement accuracy), ASTM E18 (Rockwell hardness testing), ASTM E10 (Brinell hardness testing), ASTM A956 (Leeb hardness testing), ASTM E23 & ISO 148-2 (Charpy impact testing), and more. Our expertise extends to direct and indirect verification, displacement measurement calibration, and compliance with ANSI/NCSL Z540-1-1994 standards. Whether you need certification for new or existing equipment, NextGen ensures that all units—both purchased from us and from third-party manufacturers—meet regulatory standards, delivering reliable, traceable, and audit-ready testing performance across aerospace, automotive, defense, and industrial applications.