The process involves applying a light preload to set a reference point, followed by a major load to perform the actual test. The difference in depth before and after the major load gives the Rockwell Hardness Value (HR). This approach minimizes operator influence and allows for direct digital or dial readings without the need for microscopes or detailed surface preparation.
With Regular and Superficial scales available, Rockwell testers can accurately evaluate everything from thin surface treatments to hardened steel components. All systems are built to meet global standards, including ASTM E18, ISO 6508, and GB/T 230, ensuring reliability and consistency across testing environments.
Understanding Rockwell Hardness Testing and Scale Selection
Rockwell hardness testing is a mechanical method used to evaluate how resistant a material is to indentation. It works by measuring the depth of penetration created by a specific combination of forces applied through a standardized indenter.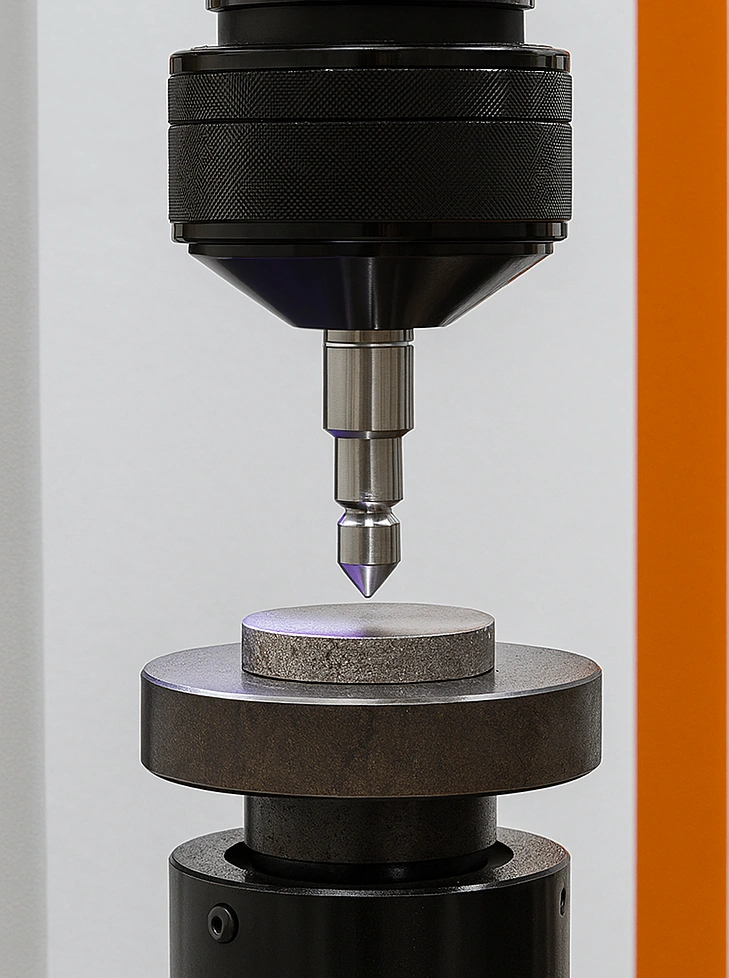
The test is carried out in two main steps. First, a preload (minor load) is applied to establish a reference point and account for surface irregularities. Then, a major load is added for a fixed period of time (dwell), creating a deeper indentation. Once the major load is removed, the depth increase is measured from the reference point and converted into a Rockwell Hardness Value.
Flexibility is one of the primary benefits of the Rockwell method. It can be adjusted to meet an extensive number of materials and testing requirements through the use of a range of available test scales. Typically, these scales are classified into two primary categories:
- Regular Rockwell: 10 kgf preload + 50, 100, or 150 kgf major load
- Superficial Rockwell: 3 kgf preload + 15, 30, or 45 kgf major load
These options allow testing of both thick and thin materials. For instance:
- HRC (diamond indenter) is ideal for hardened steel, tool components, and cast iron
- HRB (steel ball indenter) is better suited to softer materials like aluminum, brass, and copper
- Superficial scales are used for thin sheets, coatings, and parts where regular Rockwell would cause damage
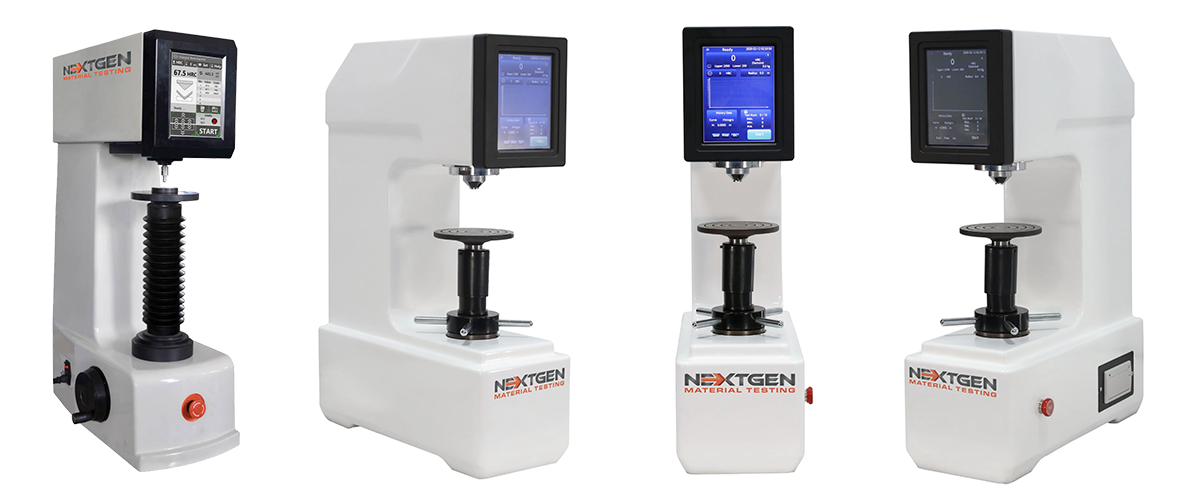
Our Rockwell Hardness Testing Equipment
At NextGen, we offer a complete line of Rockwell hardness testing systems to support a range of industrial and laboratory applications. Whether you need manual operation, fully digital automation, or advanced configurations for specialized testing, our lineup delivers the flexibility, accuracy, and reliability required for everyday quality control and in-depth material analysis.
NG-RockGen Analogue Series
The NG-RockGen Analogue Series is designed for straightforward, cost-effective hardness testing. Available in manual and electronic models, these systems are ideal for standard Rockwell Regular scale applications. Each unit provides consistent depth-based measurements and is built for long-term durability in workshop or lab environments.
NG-RockGen DGEN Series
The DGEN Series offers a fully digital solution for Rockwell Regular, Superficial, and Twin scale testing. With automatic load application, intuitive controls, and advanced digital readouts, this system is ideal for operations that require fast results, traceable data, and repeatable accuracy. It's well-suited for both high-volume production lines and detailed lab work.
GenRock NG-150 Series
The NG-150 system is built to handle complex Rockwell testing tasks with a high level of precision and flexibility. This model supports both manual and automatic modes and can be equipped with a motorized stage, Jominy end-quench testing accessories, and custom specimen fixtures. It’s an excellent choice for metallurgical labs and heat-treatment facilities looking for flexible, high-performance Rockwell testing.
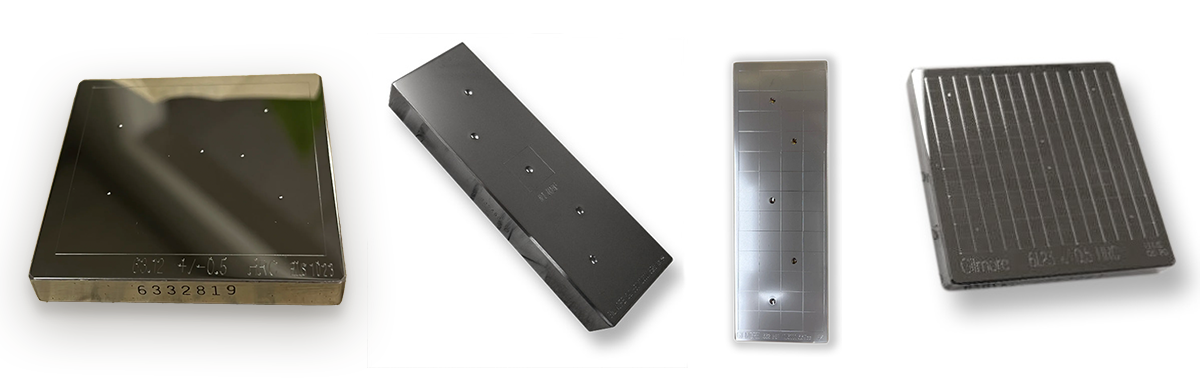
Certified Test Blocks, Indenters, and Accessories
To support consistent and traceable hardness testing, we provide a complete selection of certified Rockwell test blocks, diamond and ball indenters, and essential testing accessories. Each item is designed to meet international calibration standards and deliver reliable long-term performance on all Rockwell scales.
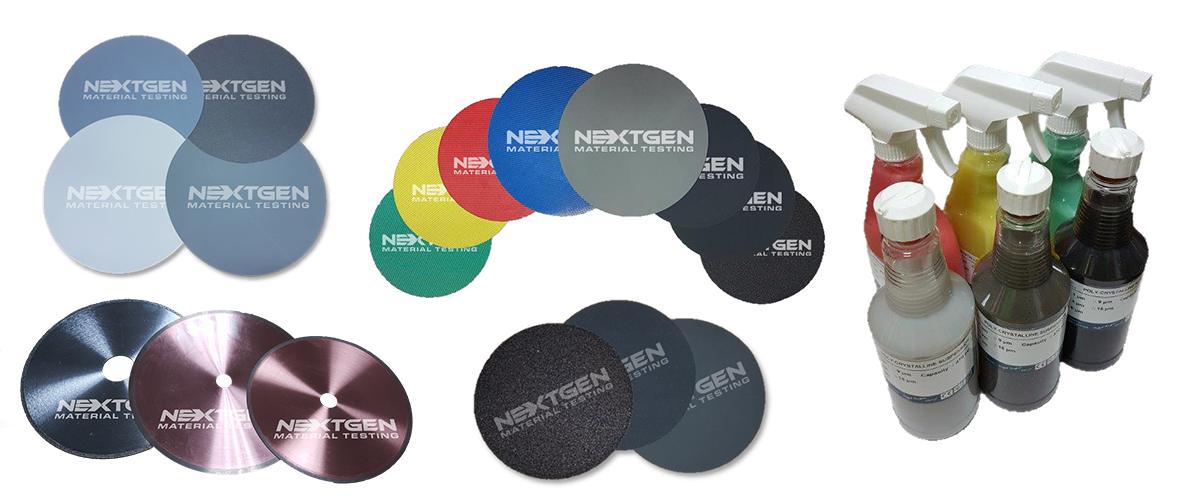
Metallography Consumables
For full sample preparation workflows, our metallographic consumables include cutting, mounting, grinding, and polishing materials. These products are compatible with all major preparation systems and ensure clean, consistent surface finishes for hardness testing and beyond.
Testing Standards We Support
NextGen’s Rockwell hardness testing systems are engineered to meet the requirements of globally recognized standards. These standards define the proper test methods, scale selection, calibration procedures, and verification processes necessary in both laboratory and production environments.
ASTM E18 – Standard Test Method for Rockwell Hardness of Metallic Materials
ASTM E18 is the primary standard for Rockwell testing in North America. It outlines the entire test process, including the use of minor and major loads, dwell times, scale definitions, and calibration protocols. This standard covers both Regular and Superficial Rockwell scales and applies to benchtop and automated hardness testers used across manufacturing, research, and quality control.
ISO 6508 – Metallic Materials – Rockwell Hardness Test
ISO 6508 serves as the international equivalent of ASTM E18 and is widely used across Europe, Asia, and other regions. The standard defines all conditions for performing Rockwell hardness tests, from machine setup and testing forces to indenter geometry and result interpretation. ISO 6508 is divided into several parts, including specifications for machine verification and calibration of hardness reference blocks.
EN ISO 6508 – Harmonized European Standard
EN ISO 6508 aligns with ISO 6508 and is fully harmonized for compliance within the European Union. It is accepted across all EU member states and is commonly required for CE-marked testing systems and internationally certified production processes.
GB/T 230 – National Standard Equivalent for Rockwell Testing
GB/T 230 defines the Rockwell hardness testing method in alignment with internationally recognized standards such as ISO 6508 and ASTM E18. It supports global manufacturing requirements and is frequently referenced in OEM and supply chain documentation for hardness compliance and verification.
ASTM E110 – Standard for Portable Hardness Testing
ASTM E110 covers the use and verification of portable Rockwell hardness testers. It defines the procedures for indirect verification when conventional methods cannot be applied, ensuring reliable hardness results in field testing environments or when working with large or assembled parts.
ASTM E140 – Hardness Conversion Tables
ASTM E140 provides official conversion guidelines between Rockwell and other common hardness scales, such as Brinell, Vickers, and Knoop. This is especially useful in labs and production settings where multiple testing methods are used, allowing for standardized comparison across results.
ISO 6308-1 – Rockwell Scale and Application Guide
ISO 6308-1 offers a detailed breakdown of Rockwell scales, including indenter types, load combinations, and material-specific use cases. It helps users choose the appropriate scale based on sample type, hardness range, and thickness, supporting proper method selection across industrial applications.
ASTM D785 / ISO 2039 – Rockwell Testing for Plastics
ASTM D785 / ISO 2039 standards adapt the Rockwell method for testing plastics and other non-metallic materials. They define alternative scale types (such as R, L, M, and E) and appropriate loading procedures for evaluating hardness in softer or more flexible components.
Industries and Applications for Rockwell Hardness Testing
Rockwell hardness testing is a trusted method for evaluating material hardness in applications where speed, consistency, and minimal surface preparation are essential. Its wide range of available scales allows it to adapt to different materials, from hardened steel to soft alloys and thin coatings. Below are the industries that rely on Rockwell testing as part of their standard quality and production workflows:
Automotive and Heavy Equipment
In the automotive sector, Rockwell testing is used to confirm the effectiveness of heat treatments applied to drivetrain components. It helps verify that parts such as axles, camshafts, and gear teeth meet strength and durability requirements before final assembly. For heavy equipment manufacturing, it’s also a quick tool for checking weld zones and cast parts without the need for complex analysis.
Aerospace and Defense
Aerospace manufacturers use Rockwell methods to assess materials for both structural and fatigue-critical applications. Components like fasteners, landing gear elements, and precision brackets are often tested on the production floor to ensure they maintain specified hardness profiles after surface treatments or forming processes. The method’s speed and repeatability make it a practical choice for these high-spec environments.
Tooling and Heat-Treatment Operations
Rockwell hardness testers are widely used in tool shops to verify the condition of tool steels after quenching or tempering. The HRC scale, in particular, offers a fast way to confirm whether punches, dies, and cutting inserts have reached their target hardness range. Superficial scales also support thin-edge inspection where traditional indentations would risk damaging the part.
Metalworking, Machining, and Foundries
In machining and foundry operations, Rockwell testing is integrated into process control. It helps validate that forgings, billets, or machined components match the expected material strength before moving to the next production stage. The method is especially useful in settings where hardness needs to be verified quickly between multiple batches or material types.
Electronics and Light Manufacturing
When working with small metal components or plated parts, superficial Rockwell scales offer an effective solution. Electronics manufacturers use the method to evaluate connector pins, enclosures, and surface finishes without risking deformation. In light manufacturing, it’s often used for quality checks on appliance frames, stamped parts, and decorative coatings.
Medical and Dental Device Production
Rockwell testers are frequently applied in medical and dental manufacturing to assess the hardness of stainless steel tools and titanium implants. The method is suited for finished components where only shallow penetration is acceptable. It’s also a reliable way to maintain batch-to-batch consistency in surgical instruments and orthopedic hardware.
Research, Education, and Materials Development
In academic settings and R&D labs, Rockwell systems provide a fast and practical approach to comparing the hardness of different metal samples or processing techniques. Students use it to learn how heat treatments influence hardness, while researchers apply it in developing new alloys or evaluating the effect of surface treatments.