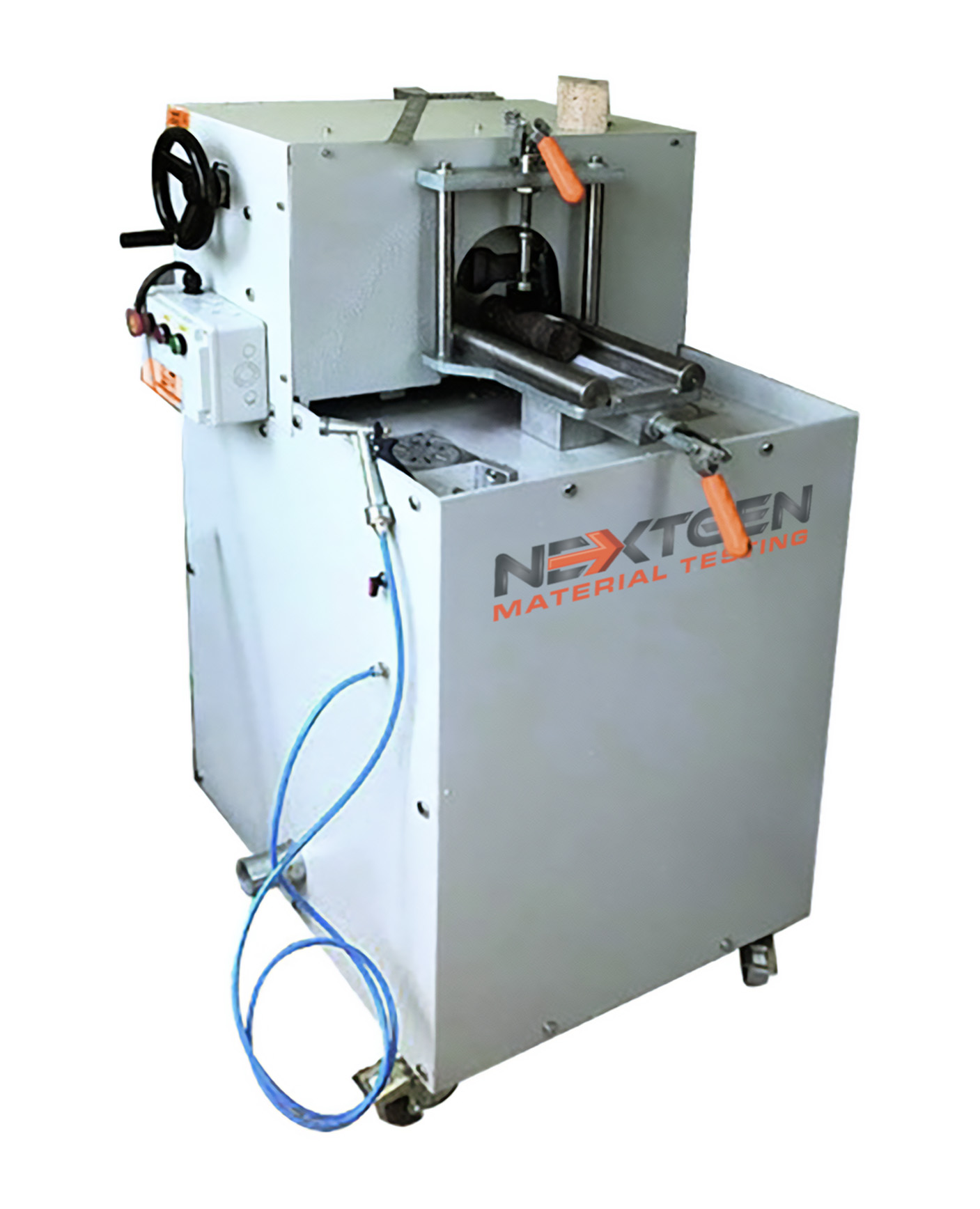
ASTM D4543, EN 12390-3, EN 12390-1, ASTM C31, ASTM C192, ASTM C617, ASTM C39
NextGen's Semi-Automatic Core Grinding Machine (also known as Coregrinder or Core Grinder) is quickly becoming the preferred alternative to the traditional rubber or sulfur capping method used by Quality Construction Labs.
Ideal for commercial testing labs and large producers, the machine can grind concrete specimens, rocks, natural stones, tiles, block pavers, and ceramic materials. It provides a safer, healthier option with superior surface finish and flatness.
This machine is a practical and efficient solution for preparing numerous cylinders for testing, reducing wait times associated with capping compounds. Read more in our newest MEGA BLOG!
Grinding wheel rotates, and the arm-wheel moves the wheel over the sample surface.
Maximum tolerance on the flatness of load-bearing surfaces is 0.050 mm for concrete samples.
Perpendicularity deviation of the side to end faces is 0.5° for core samples.
Painted steel parts to prevent corrosion.
Locking wheels for easy transport.
High-quality genuine diamond cutting wheel for an accurate, smooth finish.
In-built water spray for cleaning.
Complies with CE safety standards, including emergency stop and locking mechanism.
In-built drain filter, easily removable for cleaning and maintenance.
Model | NG-CoreGrind 1000 |
NG-0060/1 | Diamond Cutting Wheel |
NG-0061/25 | Adapters for Ø25mm (1.0”) core samples |
NG-0061/38 | Adapters for Ø38mm (1.5”) core samples |
NG-0061/50 | Adapters for Ø50mm (2”) core samples |
NG-0061/75 | Adapters for Ø75mm (3”) core samples |
NG-0061/20 | Adapters for Ø100×200mm (4” by 8”) cylinder samples |
NG-0061/15 | Adapters for Ø150×300 (6” by 12”) mm cylinder samples |
Custom Adapters like 1.875” NQ, can be ordered separately. Please advise your consultant for your specific adapter dimension requirements.
The primary purpose of the Semi-Automatic Core Grinding Machine – NG-CoreGrind 1000 is to prepare concrete, rock, and other material specimens for precise testing. This preparation involves grinding the ends of cylindrical cores or other samples to create flat, smooth surfaces that are essential for accurate and reliable testing. The machine is particularly valuable in quality control labs, research institutions, and large-scale production facilities where specimen preparation must meet strict industry standards.
By providing a consistent and superior surface finish, the NG-CoreGrind 1000 reduces the need for traditional methods such as rubber or sulfur capping, which can introduce variability and errors in testing results. This machine guarantees that the load-bearing surfaces of the specimens are within the required tolerance levels, making it crucial for tests that determine materials' mechanical properties, such as compressive strength.
Click here to learn more about the product or here to receive a personalized quote.
The Semi-Automatic Core Grinding Machine – NG-CoreGrind 1000 is designed with adaptability in mind, making it capable of grinding a broad range of materials commonly used in construction and material testing. The machine can effectively grind concrete specimens, which are crucial for testing in quality control labs to assess compressive strength and other mechanical properties. Additionally, the NG-CoreGrind 1000 is suitable for grinding rocks and natural stones.
Beyond concrete and stones, the NG-CoreGrind 1000 grinds tiles, block pavers, and ceramic materials. This makes it valuable for laboratories and manufacturers involved in the production and testing of these materials, assuring that they meet the necessary standards for durability and performance. The machine’s ability to deliver a superior surface finish and flatness enhances subsequent testing accuracy, which is critical for achieving reliable and consistent results.
Click here to learn more about the product or here to receive a personalized quote.
The Semi-Automatic Core Grinding Machine – NG-CoreGrind 1000 complies with several key industry standards that are crucial for guaranteeing material testing accuracy and reliability. These include EN 12390-3 and EN 12390-1 for concrete testing, ASTM C31 and ASTM C192 for concrete specimen preparation and curing, ASTM C617 for capping cylindrical concrete specimens, and ASTM C39 for determining compressive strength. Compliance with these standards will ensure that the machine provides consistent and reliable surface preparation.
Designed to meet these standards, the NG-CoreGrind 1000 supports quality control processes in laboratories and production facilities, making it an indispensable tool for verifying that materials meet performance and safety criteria in many industries, including construction and materials science. This compliance highlights the machine's reliability in preparing specimens critical for accurate and standardized testing.
Click here to learn more about the product or here to receive a personalized quote.
The Semi-Automatic Core Grinding Machine – NG-CoreGrind 1000 is equipped with many key features that make it a standout tool for material preparation in testing laboratories and production facilities. First, it uses a high-quality diamond cutting wheel, which ensures a precise and smooth finish on various materials, including concrete, rocks, and ceramics. The machine also features a rotating grinding wheel and an arm wheel that moves the grinding wheel over the sample surface.
Another significant feature is the in-built water spray system, which aids in cleaning the sample during the grinding process and helps maintain the machine's efficiency. The machine also includes a removable drain filter, making maintenance straightforward. For safety, the NG-CoreGrind 1000 complies with CE safety standards, featuring an emergency stop and locking mechanism, and its painted steel parts help prevent corrosion. Additionally, the machine is designed with locking wheels, allowing for easy transport and positioning within the laboratory. These features collectively contribute to the machine’s reliability, ease of use, and long-term durability.
Click here to learn more about the product or here to receive a personalized quote.
The Semi-Automatic Core Grinding Machine – NG-CoreGrind 1000 offers a variety of optional accessories that increase its versatility and functionality. Among these are diamond cutting wheels, which are essential for ensuring precision and longevity in the grinding process. Additionally, the machine can be equipped with adapters for different core sample sizes, ranging from Ø25mm (1.0”) to Ø150×300mm (6” by 12”) cylinder samples. These adapters allow the machine to accommodate a large variety of specimen sizes.
For laboratories that need to handle custom-sized samples, the NG-CoreGrind 1000 also offers custom adapters, such as the 1.875” NQ adapter, which can be ordered separately. These accessories are crucial because they allow the machine to be tailored to specific testing needs, so that it can meet the diverse demands of different industries, including construction, geology, and materials science. This flexibility makes the NG-CoreGrind 1000 a practical and efficient tool for preparing a broad range of material specimens for accurate testing.
Click here to learn more about the product or here to receive a personalized quote.
The Semi-Automatic Core Grinding Machine – NG-CoreGrind 1000 is designed with several features that significantly improve both safety and user experience. One of the key safety features is its compliance with CE safety standards, which include an emergency stop button and a locking mechanism. These features provide immediate control over the machine's operation, allowing users to quickly halt the grinding process in case of any issues, thereby minimizing accident risk.
Additionally, the machine's in-built water spray system helps control dust and debris during grinding, creating a cleaner and healthier working environment. The water spray not only aids in the grinding process but also prevents the accumulation of harmful particles in the air, which can be a significant health concern in laboratories and industrial settings.
The NG-CoreGrind 1000 also enhances the user experience with its ease of use and maintenance. The locking wheels make it easy to transport and position the machine within the workspace, providing flexibility in its use. The easily removable drain filter simplifies maintenance tasks, enabling the machine to remain in optimal working condition with minimal effort.
Click here to learn more about the product or here to receive a personalized quote.
In order to achieve a high degree of precision, the Semi-Automatic Core Grinding Machine - NG-CoreGrind 1000 is engineered to achieve a high level of flatness in the surface of loads-bearing surfaces for concrete samples. The maximum tolerance for the flatness of these surfaces is 0.050 millimeters. Having a level of precision of this level is crucial for ensuring that the prepared concrete specimens will have perfectly flat and uniform surfaces after they have been prepared.
Flatness within this tight tolerance helps to distribute loads evenly during compressive strength tests, enabling the test results to accurately reflect the material's true properties. Uneven surfaces could lead to incorrect test outcomes, potentially compromising data integrity. Therefore, the NG-CoreGrind 1000’s ability to maintain such precise flatness is key to its effectiveness in quality control and research applications.
Click here to learn more about the product or here to receive a personalized quote.
Yes, the Semi-Automatic Core Grinding Machine – NG-CoreGrind 1000 is capable of handling custom-sized core samples, making it highly adaptable to different testing needs. In addition to its standard adapters for commonly used core sizes, such as Ø25mm (1.0”) to Ø150×300mm (6” by 12”) cylinders, the machine also offers the flexibility to accommodate non-standard or custom-sized cores. For specific requirements, custom adapters like the 1.875” NQ adapter can be ordered separately.
This capability is particularly valuable for laboratories and testing facilities that deal with a wide range of material sizes and types. By allowing for custom-sized cores, the NG-CoreGrind 1000 ensures that it can meet the diverse demands of industries such as construction, geology, and materials science. As a result of this adaptability, the machine becomes an indispensable tool for precise and accurate specimen preparation across a broad spectrum of applications due to its adaptability.
Click here to learn more about the product or here to receive a personalized quote.
The Semi-Automatic Core Grinding Machine – NG-CoreGrind 1000 is designed with several maintenance-friendly features that contribute to its longevity and consistent performance. One of the key features is the in-built drain filter, which is easily removable for cleaning. This filter helps to collect debris and particles generated during the grinding process, preventing them from accumulating and potentially clogging the machine. Regular cleaning of this filter is straightforward, maintaining machine efficiency and reducing downtime.
Additionally, the machine is equipped with a water spray system that not only aids in the grinding process but also cleans the grinding area. This minimizes the build-up of dust and residue. The painted steel parts of the NG-CoreGrind 1000 are another important maintenance feature, as they are designed to prevent corrosion, thereby extending the machine’s lifespan even in environments where moisture and other corrosive elements are present.
Click here to learn more about the product or here to receive a personalized quote.
The Semi-Automatic Core Grinding Machine – NG-CoreGrind 1000 offers several advantages over traditional capping methods, such as rubber or sulfur capping, making it a superior choice for preparing concrete and other material specimens for testing. One of the key benefits is the machine's ability to produce extremely flat and smooth load-bearing surfaces with a maximum flatness tolerance of 0.050 mm. This precision eliminates the variability and potential inaccuracies that can occur with capping methods, where inconsistencies in the capping material can affect the uniformity of the specimen's surface.
Another significant advantage is the NG-CoreGrind 1000's time efficiency. Traditional capping methods often require considerable setup and curing time, which delays the testing process. In contrast, the NG-CoreGrind 1000 quickly grinds specimen surfaces, reducing preparation time and allowing faster testing cycles.
Additionally, the NG-CoreGrind 1000 improves safety and environmental conditions. Capping with sulfur, for instance, involves heating and handling hazardous materials, which pose safety risks and environmental concerns. The NG-CoreGrind 1000 grinding process is safer, cleaner, and more environmentally friendly, reducing exposure to harmful chemicals and fumes.
Click here to learn more about the product or here to receive a personalized quote.
Yes, the Semi-Automatic Core Grinding Machine – NG-CoreGrind 1000 is highly suitable for large-scale operations, particularly in commercial testing labs and production facilities that require efficient and precise preparation of multiple specimens. The machine's design is optimized for handling a high volume of samples, making it perfect for large producers and testing laboratories that need to process numerous concrete, rock, or ceramic specimens quickly and accurately.
One of the key factors that make the NG-CoreGrind 1000 suitable for large-scale operations is its semi-automatic functionality, which significantly reduces manual labor and increases productivity. The machine's ability to consistently deliver precise, flat surfaces on a wide range of materials ensures that each specimen meets the strict standards required for reliable testing, minimizing the need for rework and maximizing throughput.
Additionally, the NG-CoreGrind 1000's robust construction and maintenance-friendly features, such as the easily removable drain filter and durable diamond cutting wheel, guarantee that it can withstand continuous operation in a busy lab environment.
Click here to learn more about the product or here to receive a personalized quote.
EN 12390-3 is a European standard that specifies the method for determining the compressive strength of hardened concrete. It is one of the critical standards used in the construction industry to assess concrete materials' quality and durability. The standard outlines the procedures for preparing and testing concrete specimens, typically in the form of cylinders or cubes, to measure their ability to withstand compressive forces.
The Semi-Automatic Core Grinding Machine – NG-CoreGrind 1000 is directly relevant to this standard because it is designed to prepare concrete specimen surfaces with a high degree of precision. For accurate compressive strength testing as required by EN 12390-3, the load-bearing surfaces of the concrete specimens must be perfectly flat and parallel. The NG-CoreGrind 1000 achieves this by grinding the specimen ends to a maximum tolerance of 0.050 mm flatness.
Click here to learn more about the product or here to receive a personalized quote.
EN 12390-1 and EN 12390-3 are both European standards related to concrete testing, but they focus on different aspects of the process. EN 12390-1 concerns the preparation and physical properties of concrete test specimens, such as their shape, dimensions, and overall integrity. This standard guarantees specimen consistency.
On the other hand, EN 12390-3 focuses specifically on the method for determining the compressive strength of these prepared concrete specimens. It outlines the procedures for applying compressive force to the specimens and measuring their strength, a critical factor in assessing concrete quality and durability.
The Semi-Automatic Core Grinding Machine – NG-CoreGrind 1000 is crucial to complying with both standards. It helps meet EN 12390-1 requirements by precisely grinding concrete specimen surfaces to make sure they are flat and correctly shaped. This preparation is vital for specimens to meet the conditions outlined in EN 12390-3, where accurate compressive strength testing is performed. Thus, while EN 12390-1 makes sure the specimens are properly prepared, EN 12390-3 guarantees they are tested correctly, with the NG-CoreGrind 1000 playing a key role in both stages.
Click here to learn more about the product or here to receive a personalized quote.
The Semi-Automatic Core Grinding Machine – NG-CoreGrind 1000 is designed to comply with ASTM C31, which is the standard practice for making and curing concrete test specimens in the field. ASTM C31 outlines the procedures for creating concrete specimens that represent construction concrete. This standard guarantees that the specimens are properly prepared and cured, allowing for accurate testing of the concrete's physical properties, such as compressive strength.
The NG-CoreGrind 1000 plays a crucial role in preparing specimens for subsequent testing by verifying that their surfaces are flat, smooth, and within the specified tolerances. This preparation is vital for making certain that specimens can be accurately tested according to ASTM C31 requirements, particularly when assessing the quality and performance of concrete in various construction projects.
Click here to learn more about the product or here to receive a personalized quote.
Yes, the Semi-Automatic Core Grinding Machine – NG-CoreGrind 1000 cmoplies with ASTM C192, which is the standard practice for making and curing concrete test specimens in a laboratory environment. ASTM C192 specifies that concrete specimens are prepared under controlled conditions to produce consistent and reliable data about material properties.
The NG-CoreGrind 1000 supports this standard by providing precise grinding of specimen surfaces, so that they are flat, smooth, and within the necessary tolerances for accurate testing. Proper surface preparation is crucial under ASTM C192, as the quality of the specimen directly affects the reliability of the test results. The machine’s ability to consistently deliver properly prepared specimens guarantees that subsequent testing can accurately reflect the true characteristics of the concrete.
Click here to learn more about the product or here to receive a personalized quote.
The Semi-Automatic Core Grinding Machine – NG-CoreGrind 1000 is designed to comply with ASTM C617, which is the standard practice for capping cylindrical concrete specimens to prepare them for compressive strength testing. ASTM C617 outlines methods for verifying that concrete specimen ends are flat and parallel.
The NG-CoreGrind 1000 facilitates compliance with ASTM C617 by providing a precise grinding process that assures specimen ends are flat and smooth. This grinding process eliminates the need for traditional capping methods, such as sulfur or rubber, which can introduce variability and potential inaccuracies in testing. By grinding the specimen ends to a tight tolerance, the NG-CoreGrind 1000 ensures that the specimens are prepared according to ASTM C617 standards, leading to more reliable and accurate test results.
Click here to learn more about the product or here to receive a personalized quote.
Yes, the Semi-Automatic Core Grinding Machine – NG-CoreGrind 1000 complies with ASTM C39, which is the standard test method for determining the compressive strength of cylindrical concrete specimens. ASTM C39 is a critical standard in the construction industry as it provides procedures for accurately measuring the compressive strength of concrete, which is necessary for assessing the quality and structural integrity of concrete used in construction projects.
The NG-CoreGrind 1000 supports compliance with ASTM C39 by ensuring that the ends of cylindrical specimens are ground to be perfectly flat and parallel. This precision is crucial because uneven or improperly prepared specimen ends can lead to inaccurate compressive strength results. By grinding the specimen ends to meet ASTM C39's stringent requirements, the NG-CoreGrind 1000 guarantees that the specimens are properly prepared for testing, thereby contributing to more reliable and consistent results.
Click here to learn more about the product or here to receive a personalized quote.
NextGen's Semi-Automatic Core Grinding Machine, also known as Coregrinder or Core Grinder, is quickly gaining preference in Quality Construction Labs over traditional rubber or sulfur capping methods. The main reason for this shift is the machine's ability to deliver superior precision and consistency in preparing concrete specimens for compressive strength testing. Unlike rubber or sulfur capping, which can introduce variability and inaccuracies due to uneven surfaces or inconsistent capping material, the Coregrinder guarantees that cylindrical specimen ends are perfectly flat and parallel.
This precision reduces errors during testing and improves results reliability. Moreover, our Core Grinding Machine offers a safer and more environmentally friendly option, eliminating the need to handle potentially hazardous sulfur compounds. The machine's efficiency also reduces preparation time, making it a practical and effective solution for labs that require high standards of accuracy and consistency in their testing processes.
Click here to learn more about the product or here to receive a personalized quote.
The grinding mechanism of the Semi-Automatic Core Grinding Machine – NG-CoreGrind 1000 is designed to provide precise and consistent preparation of material specimens. The grinding wheel of the machine rotates, and this rotating action is combined with the movement of the arm wheel that guides the grinding wheel over the sample surface. This dual-action mechanism ensures that the entire specimen surface is evenly ground, resulting in a perfectly flat and smooth finish.
This process is critical for preparing specimens for accurate testing, as it ensures that the load-bearing surfaces are uniform and within the required tolerances. The machine's ability to maintain consistent pressure and movement over the specimen's surface is what makes the NG-CoreGrind 1000 a preferred choice for labs that require high precision in material testing.
Click here to learn more about the product or here to receive a personalized quote.
The Semi-Automatic Core Grinding Machine – NG-CoreGrind 1000 achieves a high level of precision in aligning the side and end faces of core specimens, maintaining a perpendicularity deviation of just 0.5°. This small deviation ensures that the ends of the specimens are nearly perfectly aligned with their sides, which is crucial for obtaining accurate and reliable test results.
In tests such as compressive strength assessments, even a slight misalignment between the side and end faces can lead to uneven stress distribution across the specimen. This could result in inaccurate data, compromising test results validity. By keeping the perpendicularity deviation to a minimal 0.5°, the NG-CoreGrind 1000 helps ensure that the specimens are properly aligned and that the testing conditions are as close to ideal as possible.
Click here to learn more about the product or here to receive a personalized quote.
The Semi-Automatic Core Grinding Machine – NG-CoreGrind 1000 provides exceptional precision in the flatness of load-bearing surfaces for concrete samples, maintaining a maximum tolerance of 0.050 mm. This level of flatness is crucial for accurate and reliable testing, particularly in compressive strength assessments, where even slight deviations in surface flatness can lead to uneven load distribution and inaccurate results.
Achieving such a tight tolerance ensures that the concrete specimen surfaces are uniformly flat, allowing for consistent and repeatable test conditions. This precision helps to minimize errors that could arise from imperfect surfaces so that the test results truly reflect the material's performance.
For laboratories and facilities that adhere to strict industry standards, maintaining a maximum flatness tolerance of 0.050 mm is necessary. The NG-CoreGrind 1000's ability to deliver this level of accuracy supports testing integrity.
Click here to learn more about the product or here to receive a personalized quote.
The Semi-Automatic Core Grinding Machine – NG-CoreGrind 1000 is designed with durability in mind, featuring painted steel parts to effectively prevent corrosion. This protective layer is essential for maintaining the machine's longevity and performance, especially in environments where exposure to moisture, chemicals, or other corrosive elements is common.
By using painted steel, the NG-CoreGrind 1000 makes sure that the machine’s structural components are shielded from rust and corrosion, which can compromise functionality over time. This protective measure not only extends the machine’s lifespan but also reduces the need for frequent maintenance or part replacements, making it a cost-effective choice for laboratories and facilities
In environments where the machine may be exposed to water or other liquids during the grinding process, the anti-corrosion properties of the painted steel are particularly valuable. They help to maintain the machine’s integrity, enabling its smooth and reliable operation even under challenging conditions.
Click here to learn more about the product or here to receive a personalized quote.
Transporting the Semi-Automatic Core Grinding Machine – NG-CoreGrind 1000 within a laboratory or testing facility is made exceptionally easy due to its built-in locking wheels. These wheels allow the machine to be moved effortlessly to different locations as needed, whether for operational convenience or storage. The ability to transport the machine smoothly is particularly beneficial in dynamic lab environments where flexibility in equipment placement is often required.
Once the machine is in the desired location, the wheels can be locked securely in place, so that it remains stable during operation. This combination of mobility and stability is crucial for maintaining the precision of the grinding process, as it prevents any unintended movement that could affect specimen preparation accuracy. The locking wheels enhance both the ease of transportation and the overall functionality of the NG-CoreGrind 1000.
Click here to learn more about the product or here to receive a personalized quote.
The Semi-Automatic Core Grinding Machine – NG-CoreGrind 1000 is equipped with a high-quality genuine diamond cutting wheel, which assists in achieving an accurate and smooth finish on a variety of material specimens. The use of genuine diamonds in the cutting wheel results in exceptional hardness and durability, allowing it to effectively grind even the toughest materials, such as concrete, rock, and ceramics, with precision.
This high-quality cutting wheel ensures that each specimen's surface is ground to a fine finish, minimizing imperfections and inconsistencies that could affect subsequent testing accuracy. The smooth finish produced by the diamond cutting wheel is crucial for preparing specimens to meet stringent industry standards, as it guarantees that the load-bearing surfaces are perfectly flat and free from irregularities.
Click here to learn more about the product or here to receive a personalized quote.
Yes, the Semi-Automatic Core Grinding Machine – NG-CoreGrind 1000 complies with CE safety standards, guaranteeing that it meets the essential health, safety, and environmental protection requirements necessary for equipment used within the European Economic Area (EEA). The machine is equipped with key safety features, including an emergency stop button and a locking mechanism. These features are crucial for preventing accidents and guaranteeing safe operation.
The emergency stop button allows the operator to immediately halt the machine’s operation in case of unforeseen issues, reducing the risk of injury or damage. The locking mechanism further enhances safety by securing the machine in place during operation, preventing unintended movement that could compromise the grinding process accuracy or pose a danger to the user.
Click here to learn more about the product or here to receive a personalized quote.
The Semi-Automatic Core Grinding Machine – NG-CoreGrind 1000 is designed with an in-built drain filter that is easily removable, significantly simplifying cleaning and maintenance. This feature is particularly helpful because it allows operators to quickly and efficiently remove debris, dust, and slurry that accumulate during the grinding process, preventing blockages and making sure the machine continues to operate smoothly.
The ease of removing and cleaning the drain filter reduces downtime, allowing the machine to be kept in optimal working condition with minimal effort. Regular maintenance of the filter ensures that the NG-CoreGrind 1000 remains effective and reliable over time, preserving grinding accuracy and extending the machine's lifespan. This user-friendly maintenance feature makes the NG-CoreGrind 1000 an ideal choice for laboratories that require both high performance and easy upkeep for material preparation equipment.
Click here to learn more about the product or here to receive a personalized quote.
Description The West Cerchar Abrasivity Index Tester is designed to determine the rock abrasivity index (CAI) for the purpose of quantifying the classification of rock materials abrasivity. This type of test is especially valuable in the mining industries, underground construction […]
Our Rock Core Cutter and Masonry Saw designed for preparing concrete, rock, or natural stone cores and test specimens.
This apparatus was originally developed at Imperial College, London, by Professor E. Hoek. It is a simple and practical method of determining the strength and slope stability of rock, both in the field and in the laboratory.
Discover the high-precision Point Load Tester for fast and reliable rock strength testing as a cost-effective solution for geotechnical and construction projects.
NG-CoreTrim is used to obtain rock samples perfectly machined (cube, prisms, etc) from irregular rock or core pieces. It is supplied complete with a proper vice to hold irregular pieces firmly in place up to 7x14
This machine is specifically used in the laboratory for cutting core samples from hard materials such as rock and concrete.
CoreGrind Double faced core grinder machine is designed to grind and polish the end surfaces of concrete & rock cube and cylinder specimens.